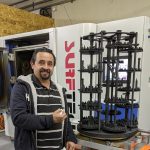
The Largest DLC Coating System Installed during COVID
March 30, 2021
DLC Coating on NHL Skate Blades
April 27, 2021Challenges to cutting Tools
Solid wood and wood-derivative materials such as plywood, fiberboard, and chipboard present a unique challenge to the cutting tool industry. Comparing with metals, wood is a special working material with high anisotropic strength, discontinuity in texture, variation in humidity, low thermal conductivity, and low heat tolerance.The design of cutting tools for woodworking features a sharp edge with a smaller wedge angle to handle the high-speed machining. In addition, the requirement of machining a massive volume of wood at high speed limits the choice of tool materials. Due to the low thermal conductivity of wood, the cutting heat cannot be dissipated through the wood chips as easy as through metal chips in the metal cutting process. It’s fair to say that the machining of seemingly soft and low-density wood and its derivatives is one of the most harsh and challenging conditions for cutting tools.
In fact, tools for all stages of woodworking processes including pruning, timbering, peeling, sawing, planning, shaping, and finishing need surface treatment to guarantee the cutting efficiency and the finishing quality of end products.
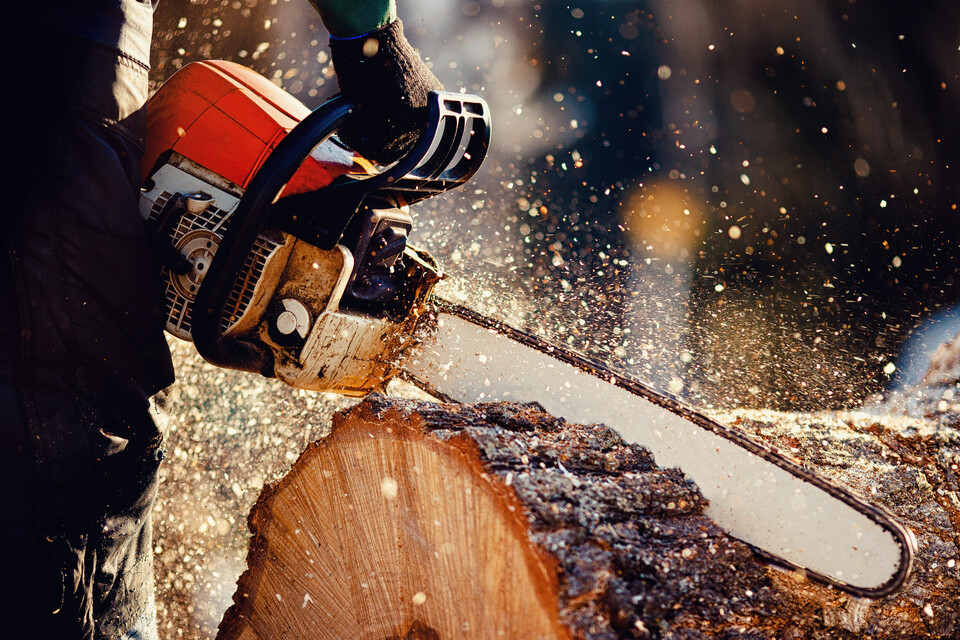
Solutions: Tool Materials, Heat-treatment & Coatings
From the materials point of view, there are three major factors governing the effectiveness of cutting tools, namely tool materials for load-bearing, heat treatment for baseline hardening, and the coating for added surface functionality of wear resistance, abrasion resistance, corrosion resistance, and a reduced friction coefficient.Tool Materials
The special features of high cutting speed, low wedge angels, the sheer size of tool geometry, and the cost grant tool steels and highspeed steels the preferred tool material of choice for woodworking. Sintered WC/Co carbides and PCD Poly Crystalline Diamond inserts are gaining popularity in selected tough applications of high-speed machining and the need for high surface finish. But, the brittleness and/or thermal properties of carbides and PCD’s pose significant restrictions on the tool geometry and working conditionsHeat Treatment
The surface hardening process of tool steels and high-speed steels through heat treatment plays an important role of cutting performance. High-speed continuous cutting generates high heat, which in conjunction with the low thermal conductivity of wood chips can create a hot zone easily exceeding 400oC near the cutting edge. A proper selection of heat treatment procedures for tool steels and high-speed steels to avoid cutting edge softening due to unexpected tempering should be assured.Coating
The protective coating is a significant value-added solution, which provides high-temperature hardness, corrosion-resistant, improved thermal conductivity, and low friction coefficient for high productivity machining without compromising the cost, machinability, and mechanical integrity of the underlying tool materials.Architecture of modern coatings for woodworking tools
Every woodworking tool can benefit from an application-specific coating. The architecture of an effective coating for woodworking tools should follow a few guidelines to achieve optimum cutting performance.- A pre-coating honing of the tool surface to properly condition the original tool surface for a better coating adhesion and the residual stress adjustment
- A thin metal interface to ensure a firm adhesion between the base material and the ceramic super-hard coating
- Choose high thermal conductivity coating materials to effectively dissipate the heat generated at the cutting edge
- A compound coating structure with either multi-layered or graded transition film configuration to reduce the risk of coating spallation due to abrupt property changes
- A surface layer of very low friction coefficient to reduce the excessive friction-induced tool heating and wear
- Keep the total compound coating thickness thin to retain the edge sharpness and to keep a sufficient thermal conduction
- A post-coating micro blasting to further increase the tool hardness and to shape the cutting-edge roundness to avoid premature edge chipping