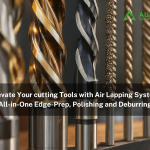
Elevate Your cutting Tools with Air Lapping System: All-in-One Edge-Prep, Polishing and Deburring
August 29, 2024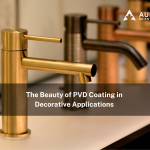
The beauty of PVD Coating in Decorative Applications
January 13, 2025In industries where flawless finishes are essential, from aerospace to medical devices, the right polishing technique can make all the difference. While traditional methods like mechanical polishing, tumbling, and electropolishing each offer unique benefits, air lapping is quickly gaining ground for its unmatched precision, efficiency, and eco-friendly qualities. This method excels in reaching intricate areas, minimizing heat impact, and achieving consistent, high-quality results, making it an ideal choice for advanced applications.
Common Metal Polishing Methods
1. Mechanical Polishing
Mechanical polishing uses rotating tools and abrasive compounds to smooth surfaces. While it’s effective for removing rough material quickly, it can be challenging to maintain tight tolerances and precision, especially on intricate parts. The process is also heat-intensive, which may cause distortion in delicate materials.
2. Tumbling and Vibratory Finishing
In tumbling, parts are placed in a rotating barrel with abrasive media to smooth rough surfaces. Vibratory finishing is similar but uses a vibrating container for faster processing. These methods are often used for bulk polishing on large volume of small parts. However, they’re not ideal for highly detailed or precision work, as the results can be inconsistent and hard to control.
3. Abrasive Blasting
Abrasive blasting uses compressed air to propel abrasive particles, removing surface material for a matte finish. This technique is fast and effective on many surfaces, but its aggressive nature makes it unsuitable for fine-polishing needs, and it can sometimes create micro-pits on the surface, which isn’t ideal for parts that require a smooth or glossy finish.
4. Electropolishing
This electrochemical process is often used to create ultra-smooth surfaces, especially on stainless steel and medical-grade components. Electropolishing can remove microscopic surface flaws and achieve mirror-like finishes. However, it involves hazardous chemicals and complex setup, limiting its practicality for many general manufacturing applications.
Air Lapping
Air lapping is a unique method that stands out among traditional polishing techniques for its precision, control, consistency and wide applications. Unlike other methods that may be rougher or less accurate, air lapping uses different grits of abrasive particles carried by compressed air to achieve precise surface finish on intricate parts. Here’s why it’s increasingly being chosen for surface polishing.
1. Simple and Fast
Air lapping delivers a surface finish 10 to 25 times faster than traditional polishing methods. Various abrasive media are available to accommodate different surface removal rates, enabling a range of surface smoothness levels. The system is easy to set up and operate, making it highly efficient.
2. No hard-to-reach areas
The abrasive particles, propelled by compressed air, can easily access even the most complex and hard-to-reach areas of intricate parts, ensuring thorough and uniform.
3. Minimal Heat Generation
Air lapping, on the other hand, produces minimal heat, protecting the structural integrity of the part and making it ideal for temperature-sensitive materials.
4. Edge Preparation and Deburring
Air lapping offers precise control over material removal, enabling the preparation of cutting edges on machining tools and effective deburring. This process enhances tool longevity and improves cutting performance.
5. Environmentally Friendly and Safe
Air lapping doesn’t rely on harsh chemicals or large volumes of media, making it a cleaner and safer choice for facilities aiming to reduce environmental impact.

Polishing
The selected polishing media can reduce surface roughness Ra for 0.1 µm or less. The polishing media can only remove very little PVD coating material (around 100 nm). The friction of the coated cutting tools after air-lapping reduces dramatically, resulting in less wear damage and longer service time in machining. As a result, the polished surface is smoothened out to bring the most shininess you can get on tools.
Deburring
Air lapping is also used to remove the sharp burrs and imperfections on the cutting tools. This deburring process would dramatically reduce the friction, improves finish and life span of the cutting tools.
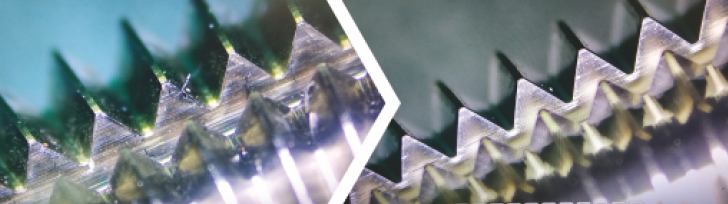
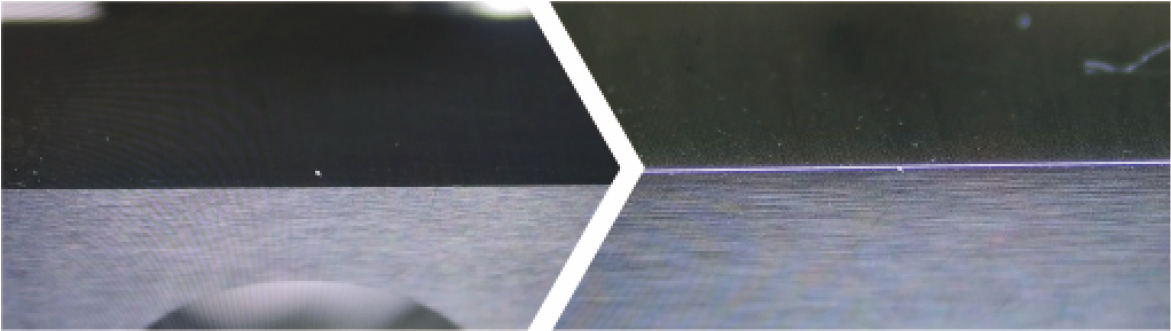
Edge Preparation
The sharp edge on the tool is slightly rounded to give it strength and prevent chipping. Air lapping can be used to round the edge of cutting tools to improve the edge strength. This process is called edge preparation. Edge preparation will also enhance the cutting chip removal in machining and prevent materials buildup on the sharp edge.
Experience the Air Lapping Advantage with Aurora Scientific Corp
Aurora Scientific Corp offers expert air lapping services and a versatile product line of air lapping systems capable of handling a wide range of sizes, materials, and geometries. Discover how our precision solutions can enhance your manufacturing process with JMAP-500BM Air Lapping System & JMAP-920BM Air Lapping System.
Contact Us